Interchangeable sector strip brushes
Interchangeable sector strip brushes
Generalities
Interchangeable sector strip brushes are used for:
- sanding wood and metal panels and frames
- cleaning conveyor belts
- brushing of large surfaces (such as formwork, etc.)
Together, they form a roller brush, however, made up of numerous linear strips with a variable B base. These strips can be replaced without dismantling the brush body, making maintenance easier and replacement much cheaper. The strips are often mounted with a slight helix α in order to make their action on the workpiece more gradual. The most classic configuration of sector strip rollers consists of a metal core with interchangeable strips mounted on welded guides. This is a particularly robust construction that allows for very heavy-duty machining.
For industrial sanding of wood, in particular doors, window frames and panels, the sandpaper roller shown in the picture (Sandy Brush) is particularly efficient.
The sanding element is suitably frayed abrasive cloth, supported in its action by a PP or buffer brush. The combination of abrasive cloth and brush provides the right rigidity and adaptability to the workpiece. With our system, it is possible to replace either the abrasive cloth only or both brushes independently, without removing the brush body from the machine and quickly. It is also possible to give a variable helical component to the strips. This is done by means of a rotor operated by means of a simple key. In this way, the user can set the most suitable propeller on Sandy Brush, either left or right. Below 500 mm brush length the rotor is not fitted. Sandy Brush can be adapted to any motor shaft diameter, within the maximum value given in the table. The brush body is made of synthetic material mounted on an aluminium tube. Configurations are possible according to the table.
Other outer diameter sizes and abrasive grits can be requested as special production. The brushing length L can be chosen as desired in multiples of 10mm.
Sandy Brush standard features
N° ELEMENTI ABRASIVI | 24 | 36 | 54 |
---|---|---|---|
DIAMETRO CORPO SPAZZOLA D1 (mm) | 120 | 180 | 280 |
DIAMETRO ESTERNO SPAZZOLA D1 (mm) | 250 | 310 | 410 |
GRANA ABRASIVA | da 100 a 320 | da 100 a 320 | da 100 a 320 |
SFRANGIATURA (mm) | 4.5 - 7 - 10 - 20 | 4.5 - 7 - 10 - 20 | 4.5 - 7 - 10 - 20 |
SPAZZOLA DI SUPPORTO | TAMPICO-PP | TAMPICO-PP | TAMPICO-PP |
LUNGHEZZA MASSIMA SPAZZOLA (mm) | 1500 | 1500 | 1500 |
DIAMETRO MASSIMO ALBERO (mm) | 40 | 60 | 60 |
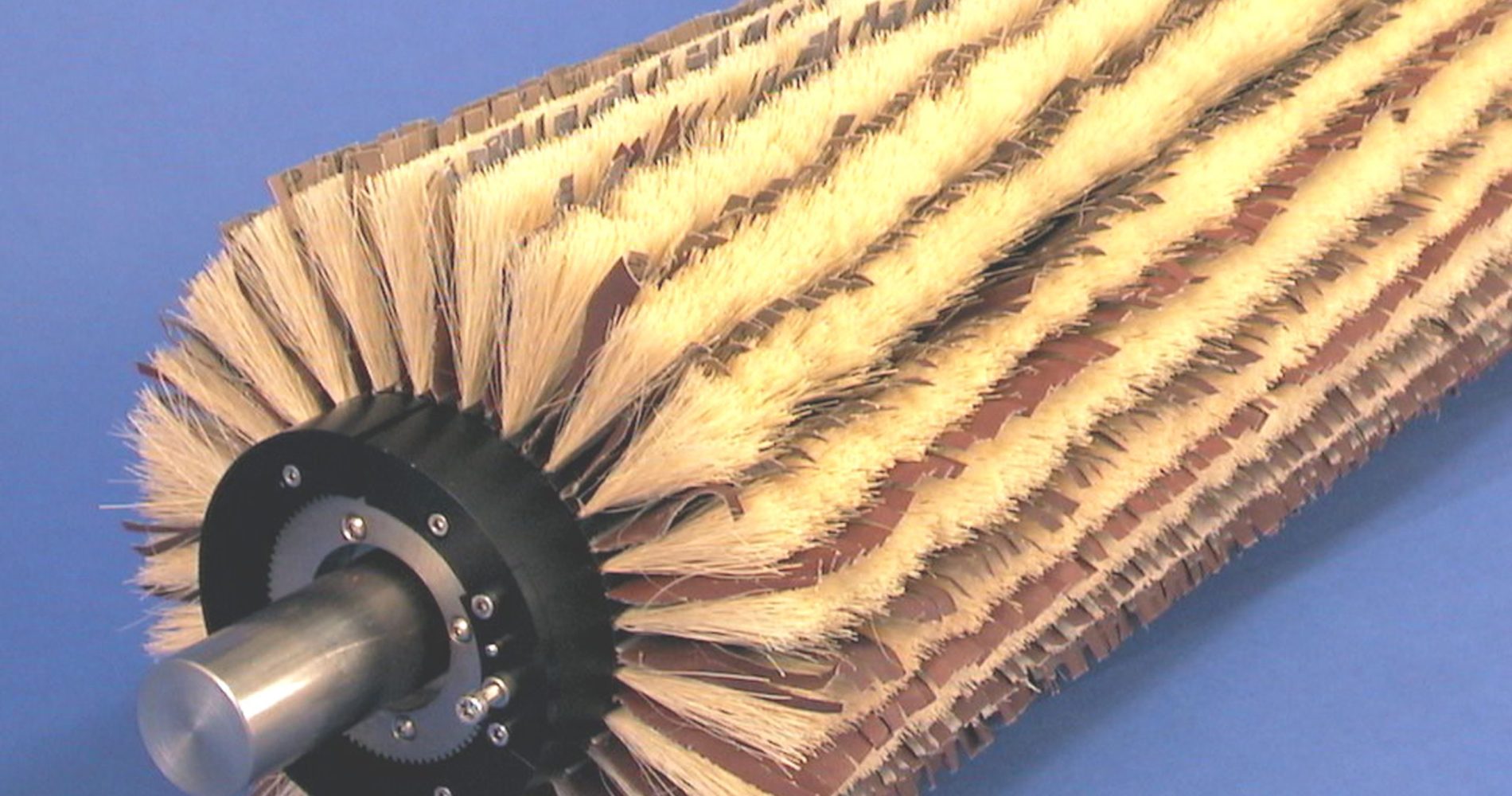
Videos and images
GALLERY
Do you want to request an offer?
Are you interested in receiving more information and being contacted by one of our specialized operators?
Request your offer now
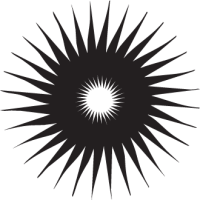
Do you want to request an offer?
Are you interested in receiving more information and being contacted by one of our specialized operators?
Request your offer now
Frequently asked questions
What is the advantage of using a brush instead of another deformable object?
The special feature of the brush is that the working surface consists of millions of individual elements, which are the ends of individual filaments.
This gives the brush an adaptability that no other element, however deformable, can have.
How much must the brush interfere with the workpiece?
It depends on various factors. In a nutshell, it can be said that 2 mm is a good compromise. The important thing is that the brush filaments work ‘on the tip’ and not on the side.
Can a bundle of filament be detached from the brush body?
Depending on the materials used and the dimensions, there is a limiting tensile load that an individual bundle can withstand.
Beyond this limit, the bundle comes off, so the brush must be calculated according to use. This limit can be greatly increased by constructing ‘sewn’ or ‘tied’ brushes by hand, where instead of a single anchoring element, a continuous steel wire is placed.
Is a punched brush or a strip cheaper?
There is no single answer. Speaking of e.g. cylindrical brushes, the strip brush is generally cheaper when the dimensions are large (e.g. over one metre in length). For small dimensions, punched brushes are certainly more suitable and convenient.
Is it possible for a single filament to slip out of the bundle and contaminate the product?
This can only happen if the brush has a manufacturing defect, like any other type of object (e.g. a roller made of silicone flakes, one of which is defective and breaks).
When it is important that no contamination occurs, synthetic (not natural) fibres with a diameter greater than or equal to 0.15 mm should be used.
What softness or hardness of brush can I achieve?
Practically all degrees of hardness are possible, from very soft to very hard. In fact, hardness is a combination of the filament diameter, its free length and the density of the bundles.
Is it possible to have a certified 'food grade' brush?
Of course, we can provide FDA or FOOD GRADE certification and filament traceability.
Is it possible to have an ATEX-certified brush?
Unfortunately not, as it is the machine + brush assembly that needs to be ATEX certified, not the brush alone.
However, it is possible to supply the materials that the certifier requires, e.g. conductive bases, conductive filaments, etc.
Is it possible to 'regenerate' a worn-out brush?
Generally speaking, it is possible, but one has to assess whether it is cost-effective, which is not always the case. In addition, in the case of a punched brush, it is inadvisable to regenerate the brush more than twice, so as not to reduce the tightness of the bundles.