Brush bodies
Brush bodies
Generalities
The filaments are attached to a rigid support that forms the ‘brush body’. The materials used are mainly synthetic, but also natural or metallic.
Materiale | PS | A | Tmax | Tmin | R | RE | RC | D | FDA | Uso prevalente |
---|---|---|---|---|---|---|---|---|---|---|
PVC | 1.40 | 0.05 | +60 | -5 | 55 | 10¹⁵ | XX | 80 | Spazzole senza particolari specifiche tecniche | |
PA | 1.13 | 10 | +95 | -30 | 70 | 10¹¹ | X | 75 | ✓ | Alimentare |
PP | 0.91 | 0.03 | +100 | 0 | 35 | 10¹⁷ | XX | 70 | ✓ | Alimentare, ambiente umido o climaticamente aggressivo, grandi spazzole a rullo |
PE | 0.96 | 0.02 | +80 | -50 | 28 | 10¹⁶ | XXX | 65 | ✓ | Grandi spazzole piane, ambiente climaticamente aggressivo |
POM | 1.41 | 0.50 | +100 | -50 | 65 | 10¹⁵ | X | 80 | ✓ | Alimentare, lavorazioni meccaniche di precisione |
PET | 1.34 | 0.50 | +110 | -20 | 55 | 10¹⁴ | XX | 80 | ✓ | Alimentare, lavorazioni precise e ambiente aggressivo |
PTFE | 2.18 | +120 | 25 | 10¹⁸ | XXX | ✓ | Alimentare, ambiente caldo | |||
PEEK | 1.32 | 0.50 | +180 | -20 | 95 | 10¹⁶ | XX | Alte temperature di esercizio | ||
PUR | 1.30 | +85 | -20 | 43 | XXX | 40 | Spazzole a cinghia | |||
LEGNO | 0.72 | 25 | +300 | 130 | 10¹² | X | 60 | Alte temperature, spazzole leggere | ||
MULTISTRATO | 0.67 | 37 | 10¹² | X | 65 | Alte temperature, spazzole lineari | ||||
CUOIO | 0.85 | 60 | +110 | -30 | - | XX | 40 | Spazzole a cinghia di grosse dimensioni | ||
ALLUMINIO | 2.70 | - | +200 | 300 | 2.8 x 10-⁶ | XX | - | Spazzole rigide ed antistatiche | ||
OTTONE | 8.50 | - | +280 | 420 | 7 x 10-⁶ | XXX | - | Corpo spazzole con elevata resistenza meccanica | ||
ACCIAIO | 7.85 | - | +450 | 500 | 1.2x10-⁵ | X | - | Spazzole motorizzate | ||
INOX | 7.90 | - | +600 | -150 | 515 | 1.2x10-⁵ | XXX | - | ✓ | Spazzole motorizzate, uso alimentare |
PS: specific weight (Kg/dm³)
A: water absorption (%)
T max: maximum operating temperature (°C)
T min: minimum operating temperature (°C)
R: tensile breaking load (N/mm²)
RE: Electrical Resistance (Ohm cm)
RC: chemical resistance (X = poor, XX = sufficient, XXX = good)
D: Hardness (ShD)
FDA: for food use according to Food and Drug Administration (U.S.A.) Room temperature only
All synthetics are available in sheets, solid and perforated bars, and in some cases also in shaped profiles.
PVC
Hto excellent processability and cold dimensional stability. However, it cannot be used in hot environments or for food use. Its deformability with temperature can be exploited to perform excellent hot-mounting of perforated bars on metal pipes.
PA (Nylon)
It has good mechanical and elastic properties, but is less workable than PVC and tends to deform during processing. It is well suited for food use (only at room temperature).
PP
It has lower mechanical properties than PA and is also available in tubes, making it suitable for the manufacture of large roller brushes, where other products would waste a lot of material. It also lends itself well to injection moulding. It resists chemicals well.
PE
As it is a soft material, it allows high processing speeds and is also relatively light, making it suitable for building large slab brushes. It also has a low coefficient of friction. It resists chemicals well.
POM(Acetal Resin)
It is a material widely used in brushes of higher technical value, as it has excellent workability, dimensional stability, temperature resistance and is suitable for food use. Available in H (homopolymer) and C (copolymer) versions.
PET
It has similar characteristics to POM, plus it has good resistance to chemicals.
PUR (polyurethane)
It is often used in the construction of belt brushes due to its deformability. It is also used as a coating for metal cores.
PTFE (Teflon)
It is used as a temperature-resistant material and when sliding on metal floors or shafts is required.
PEEK
It is a technological material that is used exclusively for its resistance to high temperatures.
Wood
Before the advent of synthetics, wood was practically the only material used to make industrial brushes. But even today, due to its ability to withstand high temperatures and its lightness, it is still a material used in technology. It is of utmost importance to use only carefully seasoned wooden boards, to avoid bending and breaking during brush work.
Multilayer
It has great dimensional stability and flatness, and has the advantage of being available in sheets of various thicknesses. Marine plywood can also work in water.
The diagram shows how a plywood board returns to normal from the situation of maximum water absorption.
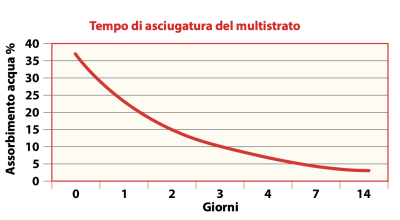
Leather
It is another material used for belt brushes, and has about the same hardness as PUR. With leather, belts of considerable width can be made, and it is often laminated with a layer of nylon or PP to increase its rigidity. The most commonly used leather is that treated with chrome.
Aluminium
It makes it possible to build very strong and light brush bodies, and at the same time is soft enough to be inset with automatic machines, albeit much faster than plastics. It has high dimensional stability. It is also an excellent electrical conductor, which is why it is also used in the manufacture of anti-static brushes.
Brass
It has high mechanical strength and great stability even at very high temperatures. It also has excellent workability.
Steel
It is mainly used as a core for roller brushes in the form of tubes, shafts, bushings, flanges. Or it is used as a body for hand-sewn brushes. There are many steel grades available for brush bodies, including stainless steel (AISI 304), in bar or plate format.
Synthetic materials have a hardness characteristic of the polymer of which they are made.
When a batch of synthetic rods or sheets enters the factory, its hardness is also checked by means of a durometer on the Shore D scale (or Shore A for softer materials such as PUR).
Hardness is also indirectly related to other characteristics such as the breaking load R. Each material has a range of acceptability, if the result falls outside this range it is rejected.
This control eliminates faults due to incorrect material manufacture, thus guaranteeing consistent quality in the supply of brushes. In the case of metal bodies, whether turned or milled, quality control is of the dimensional type; various high-precision instruments are used for this purpose.
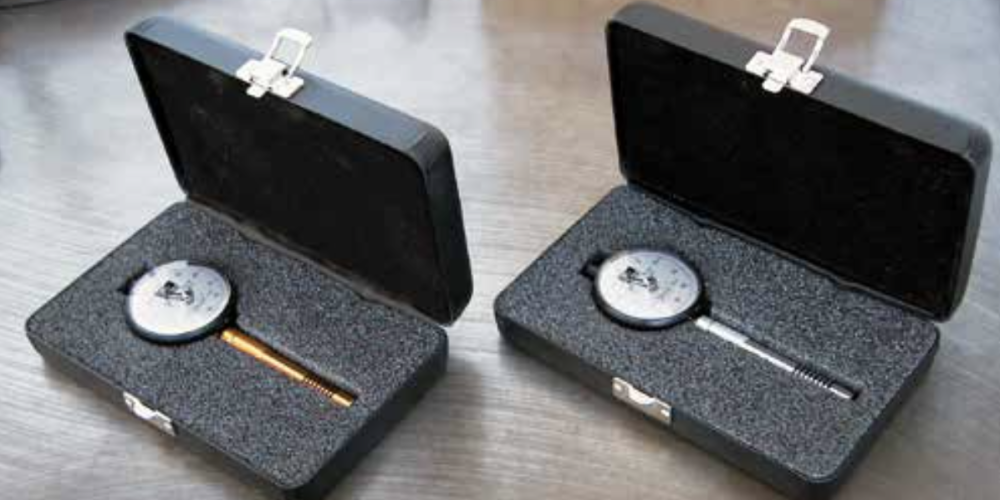
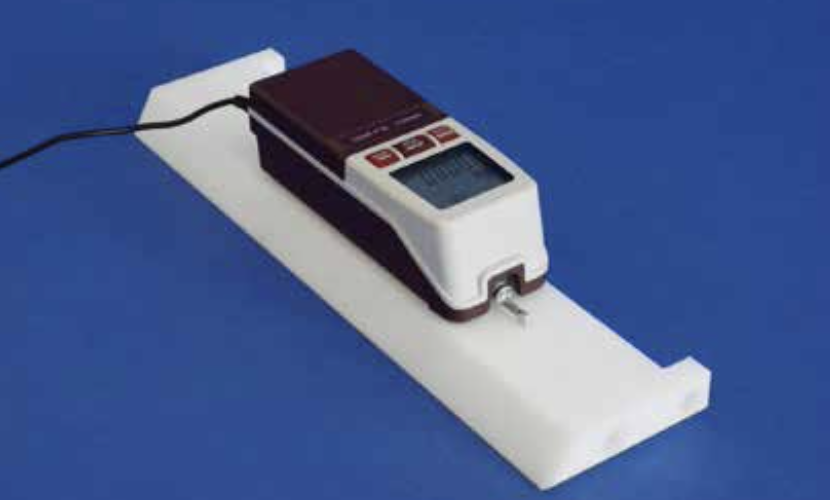
Frequently asked questions
What is the advantage of using a brush instead of another deformable object?
The special feature of the brush is that the working surface consists of millions of individual elements, which are the ends of individual filaments.
This gives the brush an adaptability that no other element, however deformable, can have.
How much must the brush interfere with the workpiece?
It depends on various factors. In a nutshell, it can be said that 2 mm is a good compromise. The important thing is that the brush filaments work ‘on the tip’ and not on the side.
Can a bundle of filament be detached from the brush body?
Depending on the materials used and the dimensions, there is a limiting tensile load that an individual bundle can withstand.
Beyond this limit, the bundle comes off, so the brush must be calculated according to use. This limit can be greatly increased by constructing ‘sewn’ or ‘tied’ brushes by hand, where instead of a single anchoring element, a continuous steel wire is placed.
Is it possible for a single filament to slip out of the bundle and contaminate the product?
This can only happen if the brush has a manufacturing defect, like any other type of object (e.g. a roller made of silicone flakes, one of which is defective and breaks).
When it is important that no contamination occurs, synthetic (not natural) fibres with a diameter greater than or equal to 0.15 mm should be used.
What softness or hardness of brush can I achieve?
Practically all degrees of hardness are possible, from very soft to very hard. In fact, hardness is a combination of the filament diameter, its free length and the density of the bundles.
Is it possible to have a certified 'food grade' brush?
Of course, we can provide FDA or FOOD GRADE certification and filament traceability.
Is it possible to have an ATEX-certified brush?
Unfortunately not, as it is the machine + brush assembly that needs to be ATEX certified, not the brush alone.
However, it is possible to supply the materials that the certifier requires, e.g. conductive bases, conductive filaments, etc.
Is it possible to 'regenerate' a worn-out brush?
Generally speaking, it is possible, but one has to assess whether it is cost-effective, which is not always the case. In addition, in the case of a punched brush, it is inadvisable to regenerate the brush more than twice, so as not to reduce the tightness of the bundles.
Filaments
Filaments
Generalities
A brush is rather special artefact. Overall, it has a well-defined geometric shape and precise dimensions, but locally, the working surface is formed by thousands or millions of small circles, which are the ends of the filaments from which the brush is made. This characteristic makes the brush different from any other mechanical element used in the technique. In fact, the working surface of a brush can be rigid or soft, oriented or isotropic, locally variable, and above all has great adaptability to the irregularities of the workpiece. Each filament behaves individually even though it is collectively part of a single working surface. The filaments are therefore the basic building blocks of the brush.
They can be of three types:
- Synthetics
- Naturals
- Metallic
Materiale | D | PS | A | Tmax | Tmin | R | RE | RC | FDA | Uso prevalente |
---|---|---|---|---|---|---|---|---|---|---|
PA 6 | 0.10-2.00 | 1.13 | 10 | +100 | -40 | 500 | 10¹¹ | X | ✓ | Alimentare, buona memoria elastica |
PA 6.6 | 0.10-2.00 | 1.14 | 9 | +120 | -40 | 550 | 10¹¹ | X | ✓ | Alimentare, ottima memoria elastica |
PA 6.12 | 0.07-2.00 | 1.06 | 3.0 | +110 | -40 | 440 | 10¹¹ | X | ✓ | Alimentare, ottima memoria elastica anche con acqua |
PA 6.12 Abrasivo | 0.50-1.60 | 1.25 | 3.0 | +110 | -40 | 440 | 10¹¹ | X | Levigatura, satinatura, finitura | |
PA HT | 0.20-0.80 | 1.18 | 3.7 | +160 | -20 | 400 | Alte temperature di esercizio | |||
PP | 0.15-3.00 | 0.89 | 0.1 | +80 | -20 | 470 | 1016 | XX | ✓ | Alimentare, anche con acqua, sollecitazione meccanica leggera |
PE | 0.30-1.00 | 0.92 | 0.1 | +70 | -50 | 170 | 10¹² | XXX | ✓ | Ambiente chimicamente aggressivo, superfici delicate |
PBT | 0.20-3.00 | 1.31 | 0.35 | +100 | -40 | 420 | XX | ✓ | Alimentare, resistenza all’abrasione anche con acqua | |
PEEK | 0.20-0.80 | 1.32 | 0.15 | +200 | 720 | XX | Alte temperature di esercizio ed elevate sollecitazioni | |||
FIBRA DI VETRO | 1.00-3.00 | 1.91 | 0.25 | +155 | 1450 | Elevata resistenza all’usura | ||||
THUNDERON | 0.03 | 1.28 | 0.8 | +150 | 5x10-¹ | Scarica elettrostatica | ||||
CRINE CAVALLO | 0.12 med | 1.00 | 50 | +150 | -150 | 10¹⁶ | Alte temperature e superfici delicate | |||
SETOLA MAIALE | 0.15 med | 1.10 | 40 | +150 | -150 | 10¹⁶ | Alte temperature, azione più incisiva rispetto al crine | |||
PELO CAPRA | 0.05 med | 1.06 | 60 | +150 | -150 | 10¹⁶ | Superfici molto delicate | |||
TAMPICO | 0.25 med | 0.86 | 35 | +160 | -150 | 10¹⁶ | Alte temperature, leggera abrasione |
|||
ACCIAIO AR | 0.12-0.70 | 7.85 | +300 | 1900 | 1.7x10-⁵ | X | Pulitura e satinatura metalli duri |
|||
ACCIAIO AAR | 0.12-0.70 | 7.85 | +300 | - | 2300 | 1.7x10-⁵ | X | Trattamento metalli con forte sollecitazione meccanica | ||
ACCIAIO INOX | 0.12-0.50 | 7.90 | +450 | 2000 | 1.7x10-⁵ | XXX | ✓ | Alimentare, ambiente umido o aggressivo |
||
ACCIAIO TEMPERATO | 0.20-0.70 | 7.85 | +350 | 2000 | 1.7x10-⁵ | X | Raschiatura meccanica profonda | |||
ACCIAIO DOLCE | 0.06-0.40 | 7.85 | +200 | 650 | 1.7x10-⁵ | X | Pulitura e satinatura metalli teneri |
|||
OTTONE | 0.06-0.30 | 8.50 | +160 | 900 | 7x10-⁶ | XX | Trattamento non aggressivo dei metalli | |||
BRONZO FOSFOROSO | 0.06-0.50 | 8.80 | +160 | 950 | 7.5x10-⁶ | XXX | Trattamento non aggressivo dei metalli, ambiente chimicamente aggressivo. Anti-scintilla |
D: filament diameter (mm)
PS: specific weight (Kg/dm³)
A: water absorption (%)
T max: maximum operating temperature (°C)
T min: minimum operating temperature (°C)
R: tensile breaking load (N/mm²)
RE: Electrical Resistance (Ohm cm)
RC: chemical resistance (X = poor, XX = sufficient, XXX = good)
FDA: for food use according to Food and Drug Administration (U.S.A.) Room temperature only.
PA (nylon) 6 / 6.6 / 6.12
Nylon (polyamide) is the most commonly used filament in technical brushes. Due to its high elastic memory, it can work under stress and then easily resume its initial configuration. It is available smooth, corrugated, white and black, in a wide variety of diameters.
PA 6.12 abrasive
The abrasive nylon is very useful in all applications that require a very aggressive filament. It consists of abrasive granules in a 6.12 nylon base. The grains can be of two types: Silicon Carbide (SC) and Aluminium Oxide (AO), which provide two different qualities of abrasive nylon. The SC filament is sharper and therefore more suitable for material removal. The AO filament has a more rounded grain and is therefore more suitable for finishing and polishing. The percentage of abrasive in nylon is on average 30%. Various grit sizes of abrasive are available (just like sandpaper) with different filament diameters (see table).
PA HT
It is a nylon-based filament that is temperature resistant up to 160°C. Available smooth in various diameters.
PP
Polypropylene has less elastic memory than nylon, but has less water absorption and greater resistance to chemicals, so it is preferable in aggressive environments. Available in many diameters up to the largest (oval mm 2×3), white, black, smooth or wavy.
PE
Polyethylene is the material that best withstands chemically aggressive environments. It is normally available smooth in the typical X-section, which gives it a gentle brushing effect, and this can be accentuated by ‘feathering’. This is the fraying of the end of each filament, achieved with a special tool. The 4 channels formed by the X-section, by capillarity, make the PE filament suitable for retaining liquids, and therefore suitable for washing delicate products, e.g. fruit.
PBT
Polyester is a very elastic filament but must not be subjected to heavy loads as it loses its mechanical properties if it reaches yield strength. It has good abrasion resistance and moderate chemical resistance.
PEEK
It is a high-tech filament that allows use at high operating temperatures of up to 200 °C. It is also suitable for high mechanical stresses. Available smooth in various diameters.
Thunderon® (Acrylic Conductor)
Thunderon is a high-tech filament. On an acrylic base, copper sulphide is chemically bonded. This results in a product with the consistency of a synthetic filament but with high electrical conductivity. It is therefore suitable for electrostatically discharging surfaces.
It has numerous advantages over carbon fibre:
- higher electrical conductivity
- carbon fibre has no consistency, whereas the Thunderon can brush the parts
- by mixing Thunderon and nylon, any desired hardness can be achieved
- while carbon fibre brushes are only available in linear form, with the Thunderon it is possible to build brushes in any shape, even rollers
Glass fibre
It is a very rigid filament whose main characteristic is that it is highly wear-resistant. Available only straight with diameters from 1 to 3 mm. It is the belief of many that the most wear-resistant fibre is carbon fibre. To verify this, we tested the two types in the laboratory by measuring their consumption on sandpaper as a function of time. From the graph in the figure, it can be seen that carbon fibre wears much faster than glass fibre
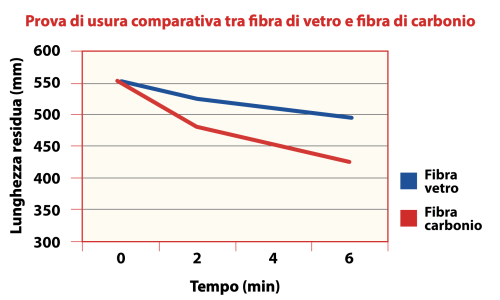
Specifications PA 6.12 Abrasive
GRANA | DIAMETRO (mm) | SEZIONE e FORMA |
---|---|---|
46 SC | 1.30 | tondo ondulato |
60 SC | 1.20 | tondo ondulato |
80 SC | 1.10 | tondo ondulato |
80 SC | 1.30 | tondo ondulato |
80 SC | 1.2x2.4 | piatto liscio |
120 SC | 0.60 | tondo ondulato |
120 SC | 1.10 | tondo ondulato |
120 SC | 1.30 | tondo ondulato |
120 SC | 1.2x2.4 | piatto liscio |
180 SC | 0.90 | tondo ondulato |
180 SC | 1.2x2.4 | piatto liscio |
240 SC | 0.80 | tondo ondulato |
320 SC | 0.60 | tondo ondulato |
320 SC | 1.2x2.4 | piatto liscio |
500 SC | 0.50 | tondo ondulato |
80 AO | 1.10 | tondo ondulato |
80 AO | 1.2x2.4 | piatto liscio |
120 AO | 1.2x2.4 | piatto liscio |
180 AO | 0.90 | tondo ondulato |
180 AO | 1.2x2.4 | piatto liscio |
320 AO | 0.60 | tondo ondulato |
320 AO | 1.2x2.4 | piatto liscio |
500 AO | 0.50 | tondo ondulato |
600 AO | 0.50 | tondo ondulato |
600 AO | 0.40 | tondo ondulato |
Horsehair
It is the most traditional material from which brushes have always been made. It is very elastic and at the same time gentle, so it can thoroughly clean the workpiece without altering its surface. Also very suitable for high temperatures and for releasing liquid films on the parts to be treated.
Pig bristle
It is slightly thicker than horsehair, and therefore a little less delicate. The filament at the origin is much shorter than horsehair, so it is not possible to make brushes with bundles longer than about 30 mm.
Goat hair
A very fine and soft filament, it is used for the treatment of the most delicate surfaces. Goat hair brushes should only graze the surface as its softness does not allow loads to be applied.
Tampico plant fibre
Dried agave is used to make Tampico (or Mexico) fibre, named after the port from which ships traditionally departed with the exotic material. It is a fibre with a characteristic yellow colour, which withstands high temperatures and also has a slightly abrasive action. Very good compounds can be made with nylon, obtaining a wide range of hardnesses.
High Strength Steel (AR)
By drawing steel, the crystalline structure of the metal is oriented in such a way as to obtain a much higher tensile strength (R) than the metal in bar form. We normally use a filament with R=1900 N/mm2. It is available corrugated, galvanised or black. The chemical composition of steel is given in the table.
Average chemical composition of AR steel
Elemento | % |
---|---|
C | 0.520 |
Mn | 0.623 |
P | 0.004 |
S | 0.010 |
Si | 0.203 |
Extra High-Resistance Steel (AAR)
It is a premium filament with R=2300 N/mm2. It is therefore suitable for high mechanical stresses, and especially for fatigue cycles, as is the case with rotary brushes. It is available corrugated, normally brass-plated.
Stainless steel
Available in AISI 304 quality and only on order in AISI 316 quality. It is widely used not only in food applications but also for surface treatments of stainless steel parts to prevent the deposit of particles that could oxidise over time.
Hardened steel
It is a very hard filament suitable for heavy scraping. It must work on point as it easily reaches fatigue fracture if bent. Only available plain.
Mild Steel (Bessemer)
It is a very soft filament with almost no elasticity. It is mainly used in very small diameters for treating delicate metal surfaces. Only corrugated is available.
Brass
It is used for cleaning especially non-ferrous metal surfaces, when less aggressiveness than steel is required. Available in different diameters and corrugated.
Phosphor Bronze
It has a similar use to brass, and is also suitable in chemically aggressive environments due to its excellent resistance. It is also used to avoid sparks during contact with surfaces.
Users of wire brushes often request technical data on the maximum loads they can be subjected to during operation. This load varies depending on the use of the brush (reciprocating/rotating motion), speed and geometry.
The problem was studied theoretically by us based on the most general working hypothesis possible, resulting in a mathematical relationship. The geometry of a rotary brush with its parameters is shown in the figure.
The values of a, l, d, n are known. However, the determination of arrow F requires the solution of some fairly complex equations. The relationships between the parameters have been summarised in diagrams such as the one shown on page. 11. The diagram refers to a friction coefficient between filament and metal surface Z=0.7, a fairly common value. It has been considered a high-strength steel. Using an inequality of the type: f (α , d, F, l, a, n) < = 1 it is possible to check whether the working angle Υ is acceptable. If the inequality is not met, it means that the load is too great and the filament breaks in a short time (fatigue cycle).
It is necessary in this case to reduce Υ. α is a filament load coefficient. Using the diagram, it is possible to obtain the value of the arrow F, or the value of the angle Υ. For reasons of overall brush efficiency, it should be noted that a Υ angle of 15° should not be exceeded.
We are available to provide you with the necessary project data.
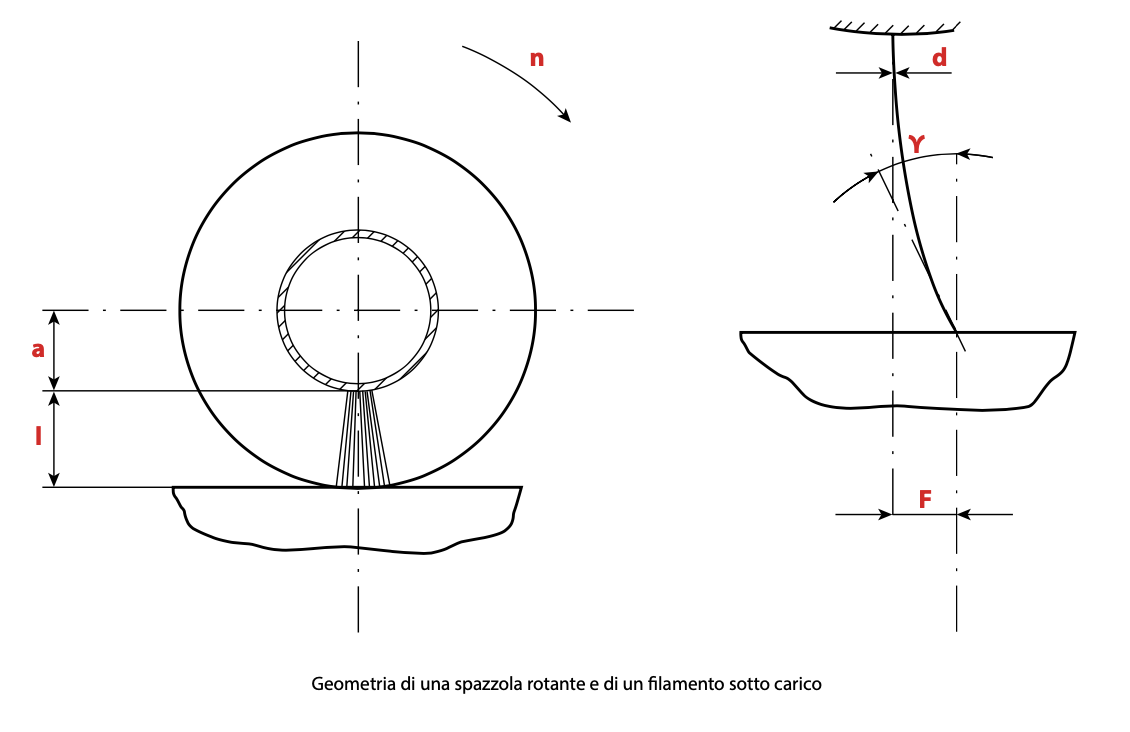
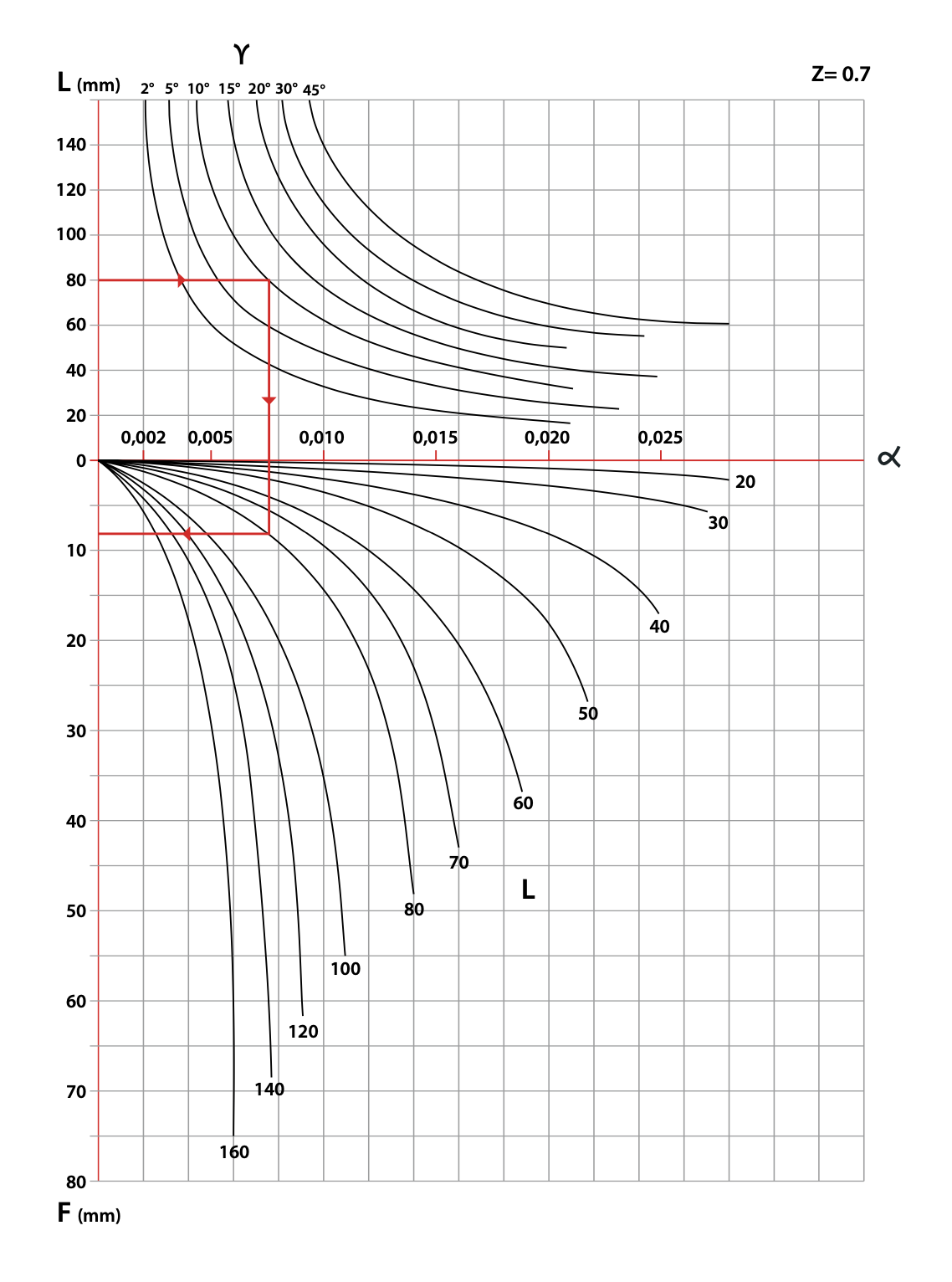
Upon arrival in the warehouse, all filament types are carefully checked, especially the diameter. In addition, their good workability is verified.
Synthetic filaments in particular have an elastic memory characteristic of the polymer of which they are made. When a batch of synthetic filament enters the company, its elasticity is also checked. For this reason, we have for many years standardised the measurement method by means of a test apparatus that loads filament samples with a known weight and then measures the springback of the filament.
Each material has a range of acceptability, if the result is outside this range the filament is rejected. This control eliminates defects due to faulty filament manufacture, thus ensuring consistent quality in brush supplies.
The filaments are often analysed under a microscope to check their level of finish. For example, this method can be used to check the correct distribution of SC or AO particles within the abrasive nylon. The method is also useful for checking the quality of a brush shave by analysing the ends of individual filaments.
Frequently asked questions
What is the advantage of using a brush instead of another deformable object?
The special feature of the brush is that the working surface consists of millions of individual elements, which are the ends of individual filaments.
This gives the brush an adaptability that no other element, however deformable, can have.
How much must the brush interfere with the workpiece?
It depends on various factors. In a nutshell, it can be said that 2 mm is a good compromise. The important thing is that the brush filaments work ‘on the tip’ and not on the side.
Can a bundle of filament be detached from the brush body?
Depending on the materials used and the dimensions, there is a limiting tensile load that an individual bundle can withstand. Beyond this limit, the bundle comes off, so the brush must be calculated according to use. This limit can be greatly increased by constructing ‘sewn’ or ‘tied’ brushes by hand, where instead of a single anchoring element, a continuous steel wire is placed.
Is it possible for a single filament to slip out of the bundle and contaminate the product?
This can only happen if the brush has a manufacturing defect, like any other type of object (e.g. a roller made of silicone flakes, one of which is defective and breaks).
When it is important that no contamination occurs, synthetic (not natural) fibres with a diameter greater than or equal to 0.15 mm should be used.
What softness or hardness of brush can I achieve?
Practically all degrees of hardness are possible, from very soft to very hard. In fact, hardness is a combination of the filament diameter, its free length and the density of the bundles.
Is it possible to have a certified 'food grade' brush?
Of course, we can provide FDA or FOOD GRADE certification and filament traceability.
Is it possible to have an ATEX-certified brush?
Unfortunately not, as it is the machine + brush assembly that needs to be ATEX certified, not the brush alone.
However, it is possible to supply the materials that the certifier requires, e.g. conductive bases, conductive filaments, etc.
Is it possible to 'regenerate' a worn-out brush?
Generally speaking, it is possible, but one has to assess whether it is cost-effective, which is not always the case. In addition, in the case of a punched brush, it is inadvisable to regenerate the brush more than twice, so as not to reduce the tightness of the bundles.