DEP120
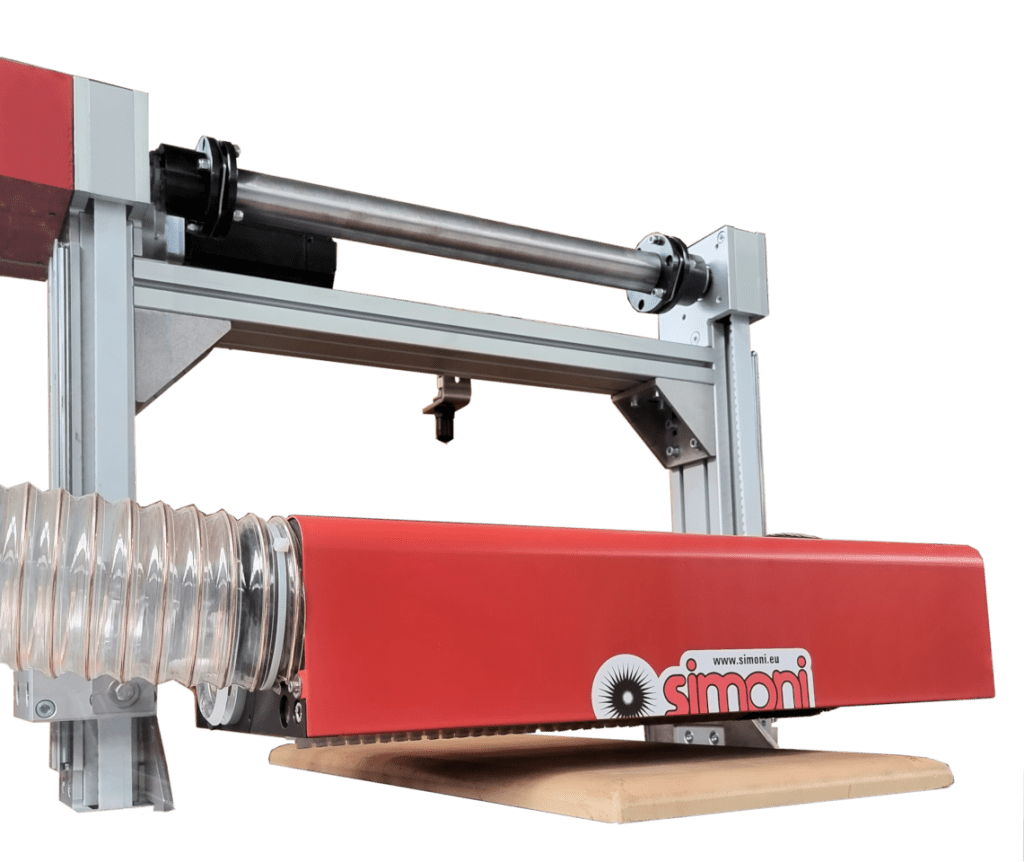
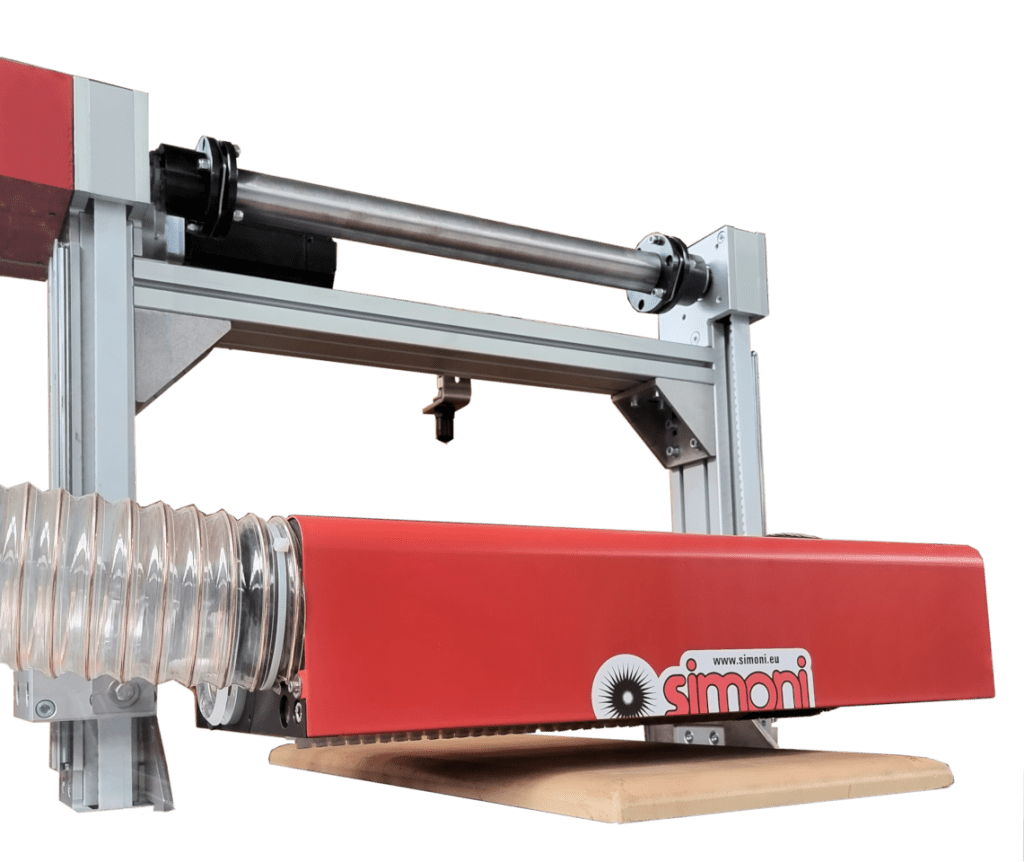
Generalità
DEP120 è un depolveratore evoluto per l’eliminazione completa delle polveri dalle superfici.
La spazzola ha diametro 120 mm ed è costituita da moduli intercambiabili da 100 mm di lunghezza. I filamenti possono variare in funzione dei materiali da trattare e del risultato da ottenere.
Il principio di funzionamento è il seguente:
- La polvere viene diselettrizzata da una barra ionizzante collegata ad un alimentatore ad alta tensione
- Una spazzola cilindrica rimuove la polvere così neutralizzata e la invia verso una cappa di aspirazione integrata nella macchina
- La cappa di aspirazione capta la polvere e la invia ad un filtro o sistema di raccolta (esterni alla macchina)
- Un soffio di aria compressa ionizzata posto dopo la spazzola produce un effetto barriera che cattura le particelle di polvere eventualmente sfuggite alla spazzola, eseguendone anche la pulizia
- Recupera automaticamente l’usura della spazzola
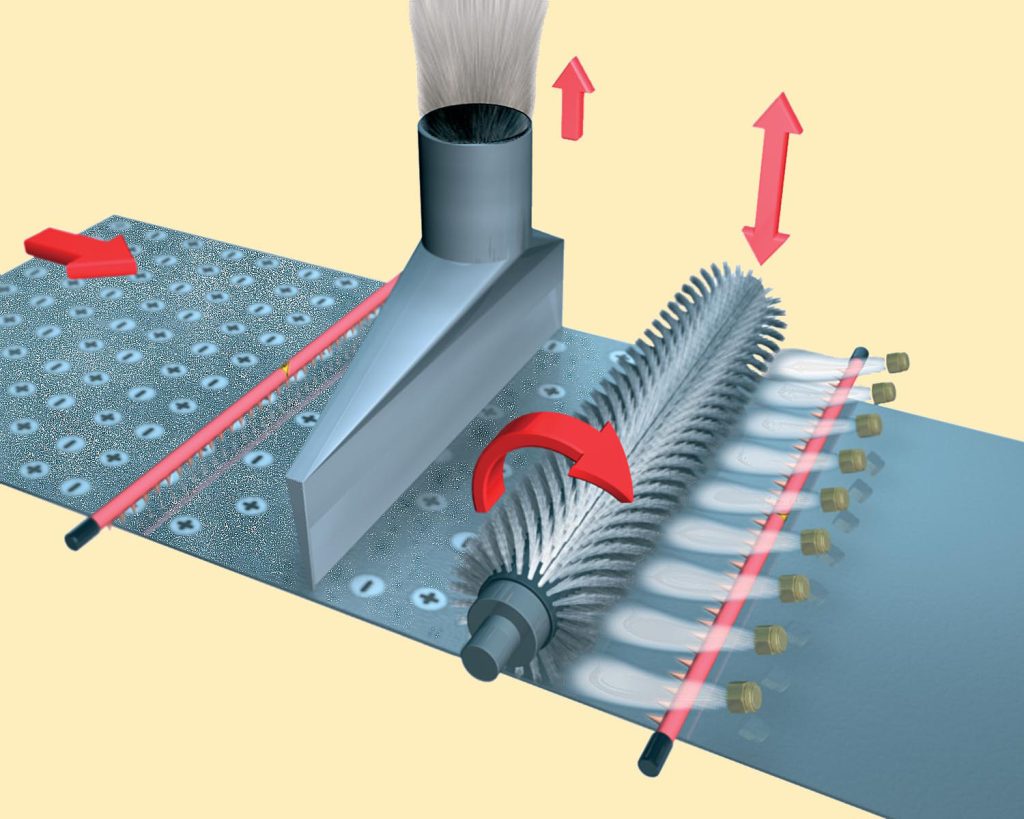
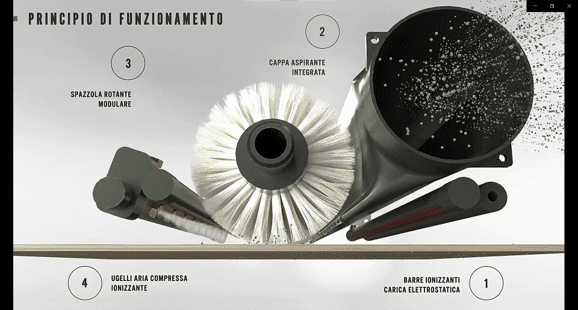
DEP120 è dotato di PLC con tastiera e display per controllare diverse funzioni:
- quota di lavoro spazzola, da 0 a 300 mm, per regolare in manuale la pressione di contatto
- velocità spazzola, da 0 a 2.000 rpm
- rotazione spazzola, avanti / indietro
- funzionamento con / senza spazzola
- adattamento automatico della quota di lavoro spazzola allo spessore del materiale da trattare con ripresa dell’usura.
- impostazione della pressione di contatto da 0 a 100 % DEP120 ha ingombri limitati, con sezione trasversale di 210 x 270 mm.
La lunghezza utile di lavoro varia da 500 a 2.000 mm. È particolarmente adatto quando si richiede una depolverazione completa della superficie.
Normalmente disponiamo di una macchina da 500 mm per eseguire test sui materiali.
CARATTERISTICHE TECNICHE | |
---|---|
SPAZZOLA | D = 120 mm L = 500 – 2000 mm V = 0 – 2000 rpm Rotazione nei due sensi |
MOTORE ELETTRICO | 230 V – 0,4 KW |
ALIMENTATORE BARRE ANTISTATICHE | Ingresso 230 V Uscita 7000 V |
VELOCITÀ DI TRATTAMENTO | max 200 m / min |
DIMENSIONI WxHxL MM | 280x130x(L+180) |
QUADRO ELETTRICO | 230 V |
ASPIRAZIONE (A CURA DEL CLIENTE) PER L=1000 MM | V=1600 mc / h P=2500 Pa |
CONSUMO ARIA COMPRESSA PER L=1000 MM P=2,5 bar | 600 NL/min |
NOTA: Le caratteristiche dell’aspirazione sono puramente indicative, variando drasticamente con la tipologia della polvere, il suo peso specifico e le condizioni ambientali (umidità, ecc.)
L’alimentazione delle barre antistatiche e l’erogazione dell’aria compressa avvengono automaticamente all’avvio della macchina.
Video e immagini
VIDEO
GALLERIA
Vuoi richiedere un’offerta?
Sei interessato a ricevere maggiori informazioni e ad essere ricontattato da un nostro operatore specializzato?
Richiedi ora la tua offerta
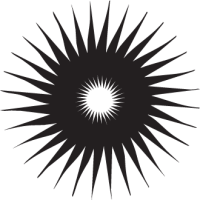
Vuoi richiedere un’offerta?
Sei interessato a ricevere maggiori informazioni e ad essere ricontattato da un nostro operatore specializzato?
Richiedi ora la tua offerta
Domande frequenti
Cosa si intende per “Macchine a spazzole”?
Sono macchine che utilizzano spazzole tecniche nel loro processo produttivo.
Quali sono le principali tipologie di macchine a spazzole?
Depolveratori, orientatori, elevatori, trasportatori.
Quali sono i vantaggi di questo tipo di macchina?
Le spazzole industriali sono caratterizzate da una grande adattabilità alle superfici, da grande flessibilità di utilizzo e varietà di forme e durezza praticamente illimitata. Per questo l’uso di spazzole nelle macchine riesce ad essere molto efficiente in numerosi processi industriali.
In particolare i depolveratori con spazzole sono più efficienti di quelli tradizionali senza contatto, mentre nel caso degli orientatori le spazzole sostituiscono altre tecniche (aria compressa, vibrazione ecc.) riuscendo a trattare i pezzi con bassi consumi energetici, in modo delicato e silenzioso. L’ingombro ridotto è un altro importante vantaggio.
Le spazzole contenute nelle macchine possono causare contaminazione del prodotto per perdita di filamento?
Può succedere solo se la spazzola si danneggia per una causa imprevedibile, come un prodotto difettoso che entra nella macchina e si incastra nella spazzola distruggendola, come d’altra parte può avvenire per ogni altro tipo di particolare presente nella macchina. Va ricordato che lo stesso tipo di spazzola viene correntemente utilizzato in campo farmaceutico ed alimentare senza problemi.
Le vostre macchine sono economicamente competitive?
Parlando dei depolveratori sono sicuramente più economiche rispetto ai principali concorrenti.
Per quanto riguarda gli orientatori sono allineati, ma se si guarda al risparmio energetico e di spazio risultano anch’essi più vantaggiosi.
Come avviene la scelta tra i vari modelli di depolveratori?
Il cliente ci invia qualche pannello (lastra, film, ecc.) che viene trattato in laboratorio con vari depolveratori, in modo da scegliere quello che dà i migliori risultati. I campioni trattati vengono poi esaminati dal cliente per approvazione.
E’ possibile testare un depolveratore prima dell’acquisto?
Generalmente abbiamo a disposizione dei depolveratori per test sul campo, che possono essere inviati al cliente per limitati periodi di tempo.
E’ necessario il vostro intervento per installare un depolveratore su una linea produttiva?
No, l’installazione viene fatta direttamente dal cliente vista la sua estrema semplicità. Naturalmente occorre prima valutare gli spazi disponibili sulla linea, che a volte contribuiscono alla scelta del depolveratore stesso.
Ogni quanto tempo occorre sostituire le spazzole?
Non esiste una risposta univoca, dipendendo questo tempo da molti fattori, come velocità del prodotto, materiali, pressione, turni di lavoro, ecc. Come indicazione di larga massima si può dire che un set di spazzole può durare tra uno e due anni, a volte di più.