Spazzole punzonate a cinghia
Spazzole punzonate a cinghia
Generalità
Disponendo i mazzetti su una base flessibile si ottiene una spazzola a cinghia, adatta per essere motorizzata tramite pulegge o tamburi. Sulle pulegge (trapezoidali o rettangolari) vanno montate spazzole di larghezza limitata, generalmente con una o due file di mazzetti. Sui tamburi si montano spazzole più larghe, con molte file di mazzetti.
Le spazzole a cinghia sono utilizzate per:
- Spazzolatura di superfici piane
- Trasporto di particolari piani
- Trasporto di oggetti tridimensionali (tappi, flaconi, ecc.) Possiamo fornire spazzole su cinghia in poliuretano (PUR), cuoio o feltro
Possiamo anche insetolare cinghie fornite dal cliente.
In questo caso va ricordato che sono realizzabili solamente spazzole su cinghie di durezza superiore a 90 Shore A. Se la base è PUR la spazzola è fornita in metratura con un unico pezzo generalmente di 30 m di lunghezza. Questo riduce considerevolmente gli sprechi al montaggio. La base di cuoio può essere disponibile anche con uno strato sottile di materiale sintetico per renderla inestensibile.
In Tabella sono riportate le misure standard per spazzole a cinghia con base PUR. Altre misure sono disponibili su richiesta. Le spazzole su cinghia di feltro sono realizzabili in dimensioni molto variabili. Rispetto al cuoio possono essere movimentate da tamburi di minore diametro dato che si tratta di un materiale più flessibile e tenero. Per gli stessi motivi, però, la tenuta meccanica dei mazzetti è inferiore a quella delle spazzole su cuoio.
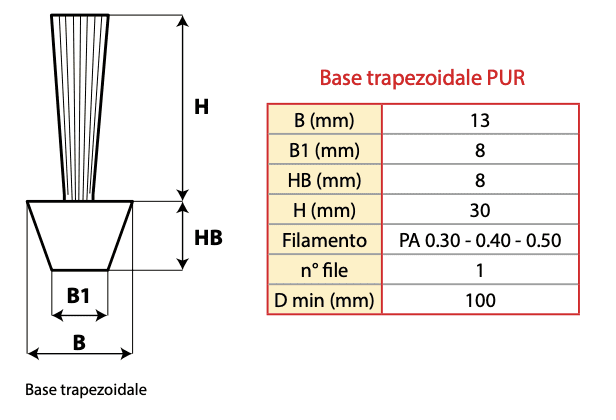
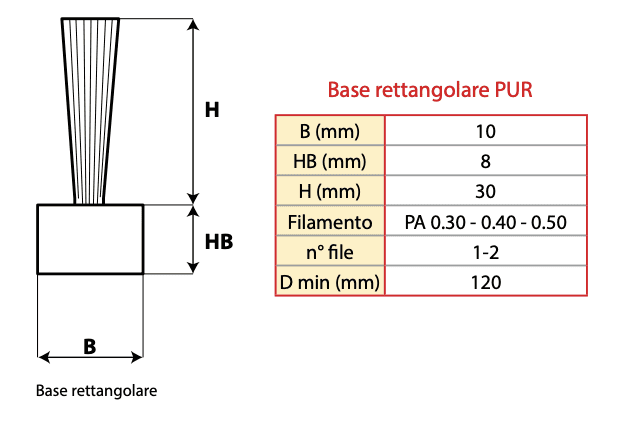
Self brush è una spazzola a cinghia su base rettangolare 7×7 mm in poliuretano.
La fornitura standard prevede la setolatura in nylon 0.30 nero ondulato con altezza 30 mm. Viene fornita in rotoli da 10 m e può essere utilizzata direttamente dal cliente per ottenere spazzole a rullo, piane o semplici guarnizioni.
Self Brush è molto utile per costruire autonomamente prototipi o per realizzare spazzole urgenti. Infatti Self Brush si taglia facilmente a misura con un normale tronchese.
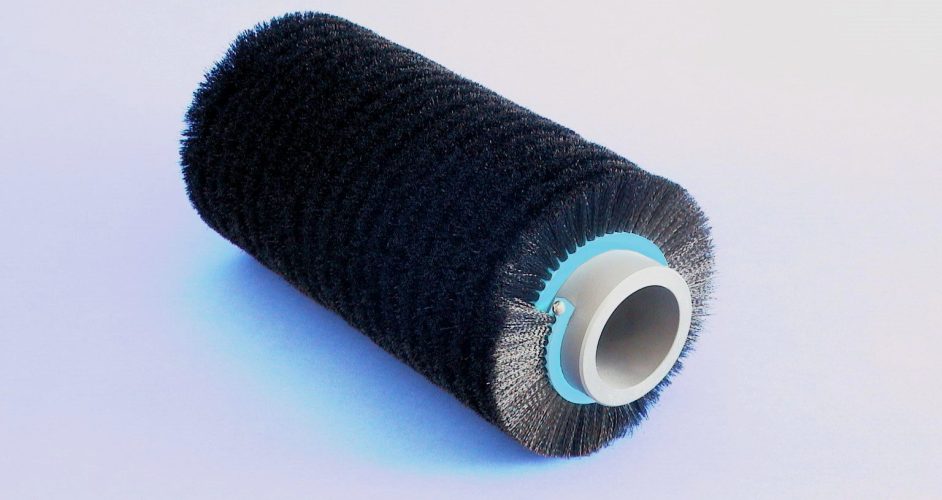
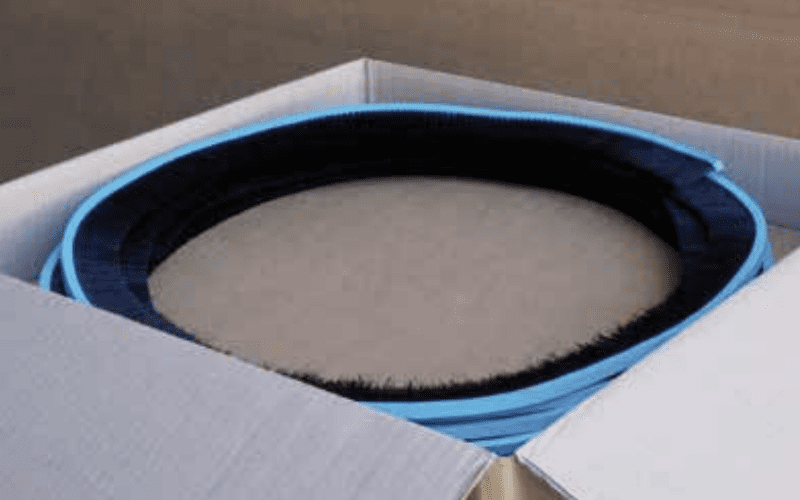
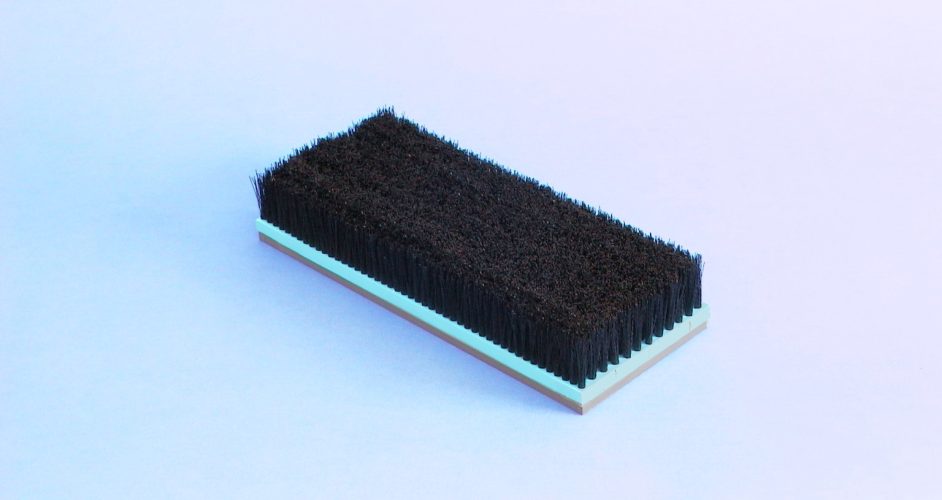
Video e immagini
GALLERIA
Vuoi richiedere un’offerta?
Sei interessato a ricevere maggiori informazioni e ad essere ricontattato da un nostro operatore specializzato?
Richiedi ora la tua offerta
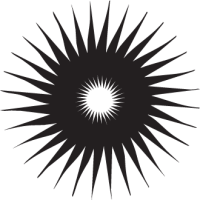
Vuoi richiedere un’offerta?
Sei interessato a ricevere maggiori informazioni e ad essere ricontattato da un nostro operatore specializzato?
Richiedi ora la tua offerta
Domande frequenti
Qual è il vantaggio di usare una spazzola invece di un altro oggetto deformabile?
La caratteristica peculiare della spazzola è che la superficie di lavoro è costituita da milioni di elementi singoli, che sono l’estremità dei singoli filamenti.
Questo conferisce alla spazzola una adattabilità che nessun altro elemento, per quanto deformabile, può avere.
Quanto deve interferire la spazzola sul pezzo da lavorare?
Dipende da vari fattori. In estrema sintesi si può dire che 2 mm è un buon compromesso. L’importante è che i filamenti della spazzola lavorino “di punta” e non sul fianco.
Un mazzetto di filamento si può staccare dal corpo spazzola?
A seconda dei materiali usati e delle dimensioni, esiste un carico limite a trazione che un singolo mazzetto può sopportare.
Oltre questo limite il mazzetto si stacca, quindi la spazzola va calcolata a seconda dell’utilizzo. Si può aumentare moltissimo questo limite costruendo spazzole “cucite” o “legate” a mano, dove invece che un elemento di ancoraggio singolo si mette un filo di acciaio continuo.
È più economica una spazzola punzonata o una strip?
Non c’è una risposta univoca. Parlando ad es.di spazzole cilindriche la spazzola strip è in genere più economica quando le dimensioni sono importanti (es.oltre il metro di lunghezza). Per piccole dimensioni le spazzole punzonate sono sicuramente più adatte e convenienti.
È possibile che un singolo filamento si sfili dal mazzetto contaminando il prodotto?
Può succedere solo se la spazzola ha un difetto di fabbricazione, come d’altra parte ogni altro tipo di oggetto (ad es. un rullo fatto con lamelle di silicone di cui una è difettosa e si spezza).
Quando è importante che non avvenga alcuna contaminazione è opportuno utilizzare fibre sintetiche (non naturali) con diametro maggiore o uguale a 0.15 mm.
Quale morbidezza o durezza di spazzola posso ottenere?
Praticamente si possono avere tutti i gradi di durezza, da morbidissima a durissima. Infatti la durezza è data dalla combinazione tra il diametro del filamento, la sua lunghezza libera e la densità dei mazzetti.
È possibile avere una spazzola certificata “alimentare”?
Certamente, possiamo fornire certificazioni FDA o FOOD GRADE e rintracciabilità del filamento.
È possibile avere una spazzola certificata ATEX?
Purtroppo no, in quanto è l’insieme macchina + spazzola a dover essere certificata ATEX, non la sola spazzola.
E’ comunque possibile fornire i materiali che il certificatore richiede, ad es. basi conduttive, filamenti conduttivi ecc…
È possibile “rigenerare” una spazzola consumata?
In linea generale è possibile, bisogna però valutare se è economicamente conveniente, e non sempre lo è. Inoltre, nel caso di una spazzola punzonata, è sconsigliabile rigenerare la spazzola più di due volte per non ridurre la tenuta dei mazzetti.