Spazzole ad anello
Spazzole ad anello
Generalità
Sono spazzole costituite da filamenti disposti attorno ad un anello metallico interno, e pressati tra due ghiere anch’esse metalliche (vedi Figura). Ne risulta una spazzola dalla forma di disco sottile con flangiatura e foro circolare. La caratteristica principale degli anelli è la modularità. Infatti essi possono essere utilizzati singolarmente, ma più spesso vengono montati su albero uno a fianco dell’altro fino a formare una spazzola a rullo. La densità del rullo può essere modificata interponendo tra i singoli anelli opportuni distanziali. Gli anelli sono elementi semplici e molto leggeri, utili quando si necessiti di un rullo di piccolo diametro e particolarmente compatto. Va comunque rilevato che l’operazione di pressatura non consente di ottenere tolleranze meccaniche strette né un’assoluta uniformità del filamento. La precisione dimensionale dell’anello è pertanto inferiore a quella di un analogo elemento punzonato.
Le spazzole ad anello sono utilizzate per :
- Elementi spazzolanti sottili (4-7 mm)
- Piccoli rulli compatti
- Rulli dove è richiesta l’intercambiabilità degli elementi spazzola
Il diametro esterno degli anelli teoricamente non è limitato. Occorre però tenere conto che, avendo l’anello un nucleo metallico relativamente piccolo, filamenti molto lunghi tendono a flettersi. In pratica si può considerare che il diametro massimo sia attorno a 500 mm con filamenti molto grossi.
Il diametro minimo è funzione della dimensione D3 della ghiera, che si può rilevare dalla Tabella con riferimento alla Figura. I valori dello spessore S sono indicativi.
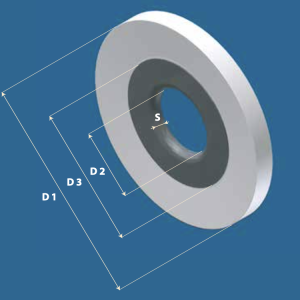
Dimensioni spazzole ad anello (mm)
D2 | 10 | 16 | 25 | 28 | 30 |
---|---|---|---|---|---|
D3 | 24 | 33 | 50 | 60 | 60 |
S | 4 | 5 | 6 | 7 | 7 |
D1 | <100 | <200 | <300 | <400 | <500 |
Video e immagini
GALLERIA
Vuoi richiedere un’offerta?
Sei interessato a ricevere maggiori informazioni e ad essere ricontattato da un nostro operatore specializzato?
Richiedi ora la tua offerta
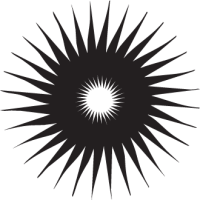
Vuoi richiedere un’offerta?
Sei interessato a ricevere maggiori informazioni e ad essere ricontattato da un nostro operatore specializzato?
Richiedi ora la tua offerta
Domande frequenti
Qual è il vantaggio di usare una spazzola invece di un altro oggetto deformabile?
La caratteristica peculiare della spazzola è che la superficie di lavoro è costituita da milioni di elementi singoli, che sono l’estremità dei singoli filamenti.
Questo conferisce alla spazzola una adattabilità che nessun altro elemento, per quanto deformabile, può avere.
Quanto deve interferire la spazzola sul pezzo da lavorare?
Dipende da vari fattori. In estrema sintesi si può dire che 2 mm è un buon compromesso. L’importante è che i filamenti della spazzola lavorino “di punta” e non sul fianco.
Un mazzetto di filamento si può staccare dal corpo spazzola?
A seconda dei materiali usati e delle dimensioni, esiste un carico limite a trazione che un singolo mazzetto può sopportare.
Oltre questo limite il mazzetto si stacca, quindi la spazzola va calcolata a seconda dell’utilizzo. Si può aumentare moltissimo questo limite costruendo spazzole “cucite” o “legate” a mano, dove invece che un elemento di ancoraggio singolo si mette un filo di acciaio continuo.
Che potenza devo prevedere per motorizzare una spazzola cilindrica?
A pagina 23 del nostro catalogo si trovano i diagrammi che rispondono a questa domanda.
È possibile che un singolo filamento si sfili dal mazzetto contaminando il prodotto?
Può succedere solo se la spazzola ha un difetto di fabbricazione, come d’altra parte ogni altro tipo di oggetto (ad es. un rullo fatto con lamelle di silicone di cui una è difettosa e si spezza).
Quando è importante che non avvenga alcuna contaminazione è opportuno utilizzare fibre sintetiche (non naturali) con diametro maggiore o uguale a 0.15 mm.
Quale morbidezza o durezza di spazzola posso ottenere?
Praticamente si possono avere tutti i gradi di durezza, da morbidissima a durissima. Infatti la durezza è data dalla combinazione tra il diametro del filamento, la sua lunghezza libera e la densità dei mazzetti.
È possibile avere una spazzola certificata “alimentare”?
Certamente, possiamo fornire certificazioni FDA o FOOD GRADE e rintracciabilità del filamento.
È possibile avere una spazzola certificata ATEX?
Purtroppo no, in quanto è l’insieme macchina + spazzola a dover essere certificata ATEX, non la sola spazzola.
E’ comunque possibile fornire i materiali che il certificatore richiede, ad es. basi conduttive, filamenti conduttivi ecc…
È possibile “rigenerare” una spazzola consumata?
In linea generale è possibile, bisogna però valutare se è economicamente conveniente, e non sempre lo è. Inoltre, nel caso di una spazzola punzonata, è sconsigliabile rigenerare la spazzola più di due volte per non ridurre la tenuta dei mazzetti.